最先端ロボットは匠の技を支えるためにある。金子眼鏡が鯖江で起こした"産業革命"
世界屈指の眼鏡産地である福井県鯖江市。多くて200にも及ぶ眼鏡づくりの各工程を専門とする工場や職人たちの分業によって栄えてきました。この地で2006年に自社一貫生産をはじめた金子眼鏡は、最先端のロボットを導入し、工程の8割を占めていた人の手による研磨作業に革命を起こしました。その目的は、手仕事をなくすことではなく、むしろ逆。伝統的な職人の技術を支えるためだというのです。
【後編はこちら】「私たちは眼鏡をつくっている」 シンプルな言葉の真意とは。金子眼鏡が、磨きに込める美意識
日本製眼鏡フレームの約96%を生産している産地の中心、福井県鯖江市。1905(明治38)年、農閑期の副業として始まったという鯖江の眼鏡づくりの歴史を象徴するかのように、黄金色に輝く稲穂に囲まれた約3500平方メートルの敷地に、その工場はありました。
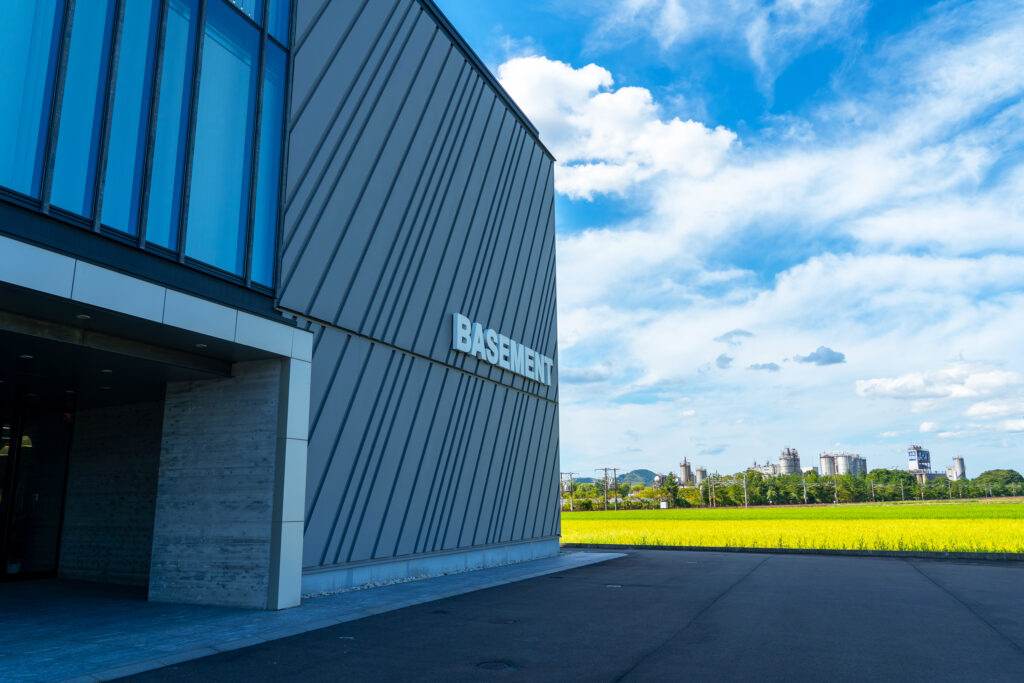
Seigo Ito
金子眼鏡が2019年に設立した自社工場「BASEMENT」。最先端のロボットを導入し、日本で初めて「マシンメイドとハンドメイド」「ハイテクとローテク」を融合させたものづくりを確立した、先進的な製造拠点です。
ロボットアームが眼鏡を磨く
全面ガラス張りのフロアには、大きな機械が整然と並んでいます。プラスチック製フレームの外形と内形を切り出す機械、つるの部分を切削する機械、丁番の穴開けや彫刻をする機械、すべてがコンピュータ制御によるものです。
中でも目を引くのが、器用にアームを操っている研磨ロボット。アームの先にある円盤型の研磨機が台の上を小刻みに行き来しながら、幅数センチに満たない眼鏡のつるを1本ずつ磨いています。
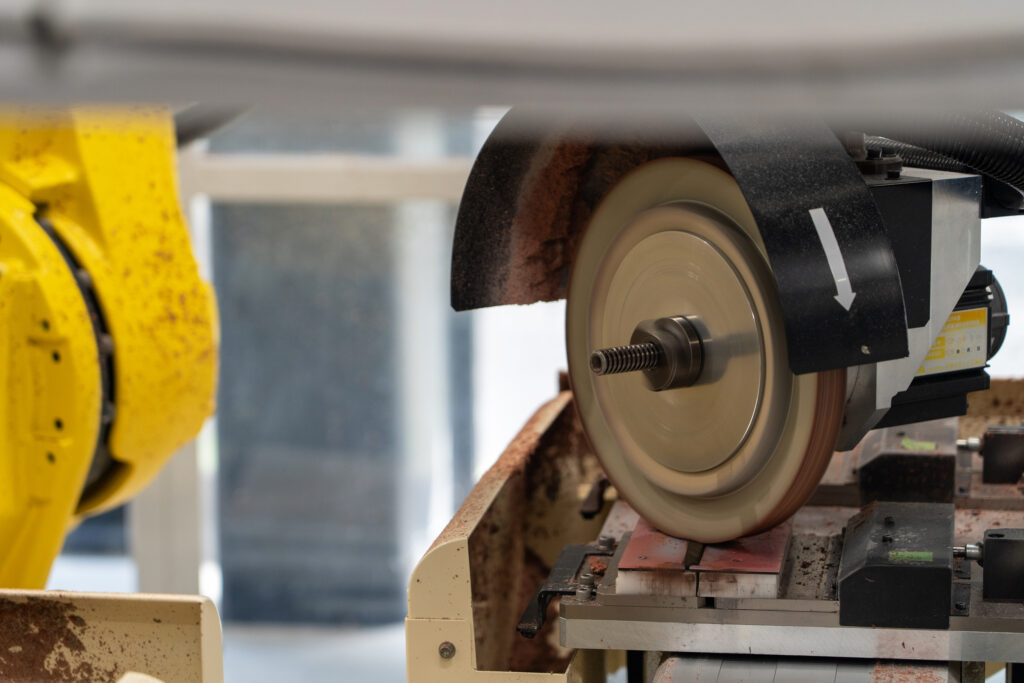
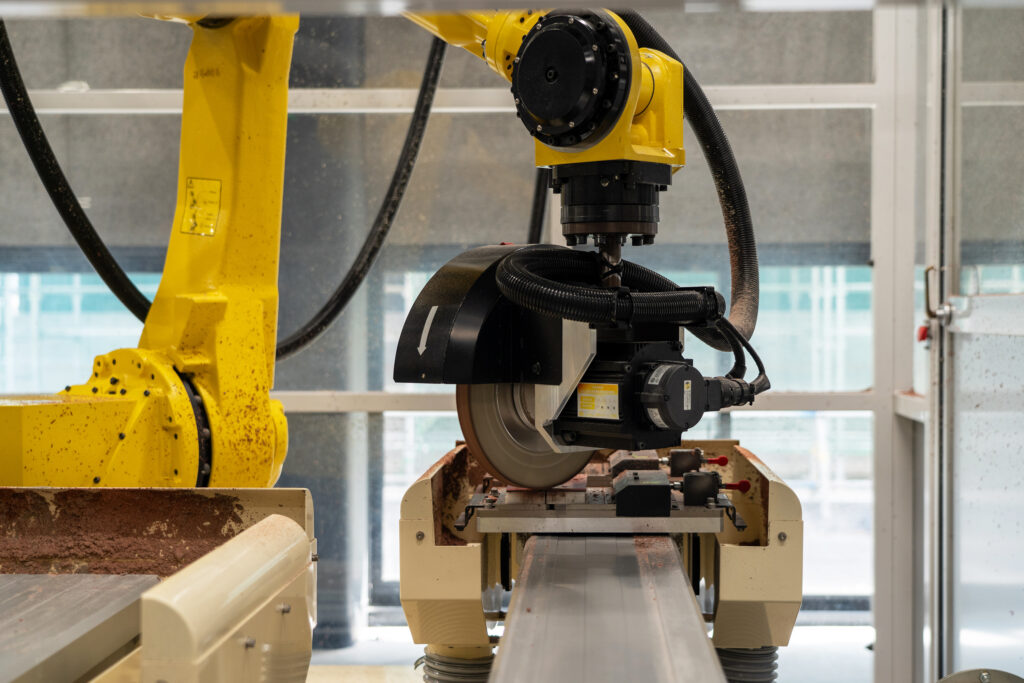
取締役で生産管理部部長の市川純一郎さんは、ロボットを導入した経緯をこう話します。
「楽器を磨くロボットを展示会で見たときに、眼鏡の研磨に応用できないかと考え、カスタマイズして導入しました。その後、より繊細にプログラミングできる別のロボットも導入し、研磨作業の自動化に成功しました」
BASEMENTでロボットたちが休みなく作業を続ける一方、車で10分ほどの距離にある拠点工場「BACKSTAGE」では、職人たちが一つひとつ手作業で眼鏡づくりをしていました。
金子眼鏡ではこの2つの工場で、機械と手仕事の両方によってプラスチックフレームを一貫生産するほか、もう一つの工場「GLASSWORKS」でメタルフレームを内製し、年間約12万本の眼鏡を国内外に送り出しています。
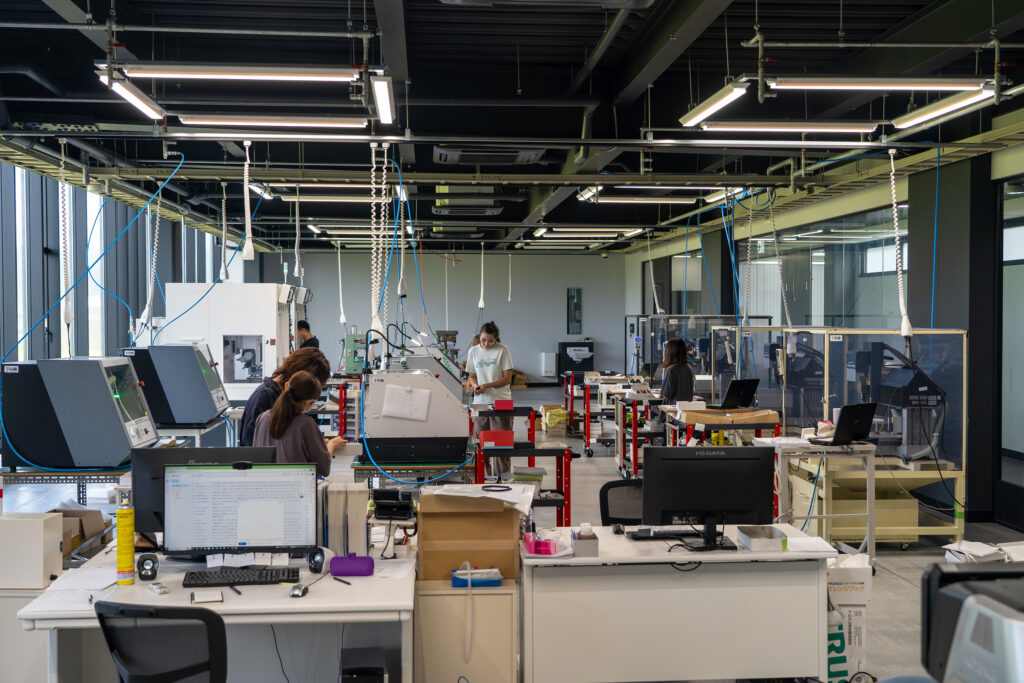
Seigo Ito
個性のある眼鏡を
眼鏡は、プラスチックフレームで約30、メタルフレームで約200の工程を経て完成します。鯖江にはそれぞれの工程を専門とする工場や熟練の職人がおり、分業によって工程ごとの技術を高め合い、世界屈指の眼鏡産地として栄えてきました。
匠の技を誇る産地において、自社一貫生産やロボット導入は極めて異色の取り組み。しかも、もともと小さな卸売業者だった金子眼鏡が製造業に参入したのは2006年のこと。20年も経たない間に"産業革命"を起こしたのです。
「1958年の創業時は、鯖江でつくられた眼鏡を分けてもらって売る、小さな二次卸でした。大手の問屋が幅をきかせている都市部を避けて地方を回り、それこそ富山のくすり売りのように24泊25日くらいで行商していたと聞いています」
取締役で店舗事業部長の大橋法明さんは、創業の歴史をこう説明します。
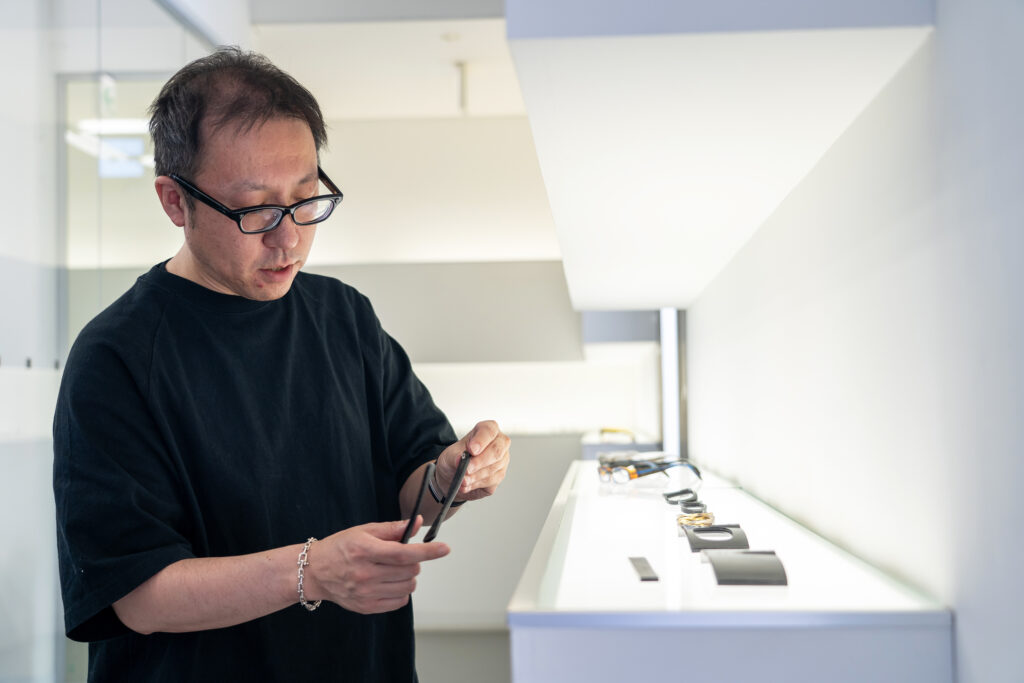
Seigo Ito
現社長で2代目の金子真也さんは、家業を継ぐ条件で東京の大学に進学。1981年に卒業して鯖江に戻り、そうした地方回りの営業を続ける中で限界を感じるようになりました。
当時は、ライセンスブランド全盛期。眼鏡メーカーは欧米の有名ブランドにライセンス料を払い、眼鏡にブランド名を刻んで販売していました。ロゴがなければどのブランドかわからないような個性のないデザインや販売方法に違和感を覚えた金子さんは「自分がかっこいいと思う眼鏡をつくりたい」と自らデザインを学び、オリジナルブランドを誕生させました。
「1980年代は量販店やチェーン店のものではないおしゃれな眼鏡を求めて、原宿や渋谷に小売店ができ始めていた頃でした。タレントの着用で話題になり、自社ブランドが躍進していきました」(大橋さん)
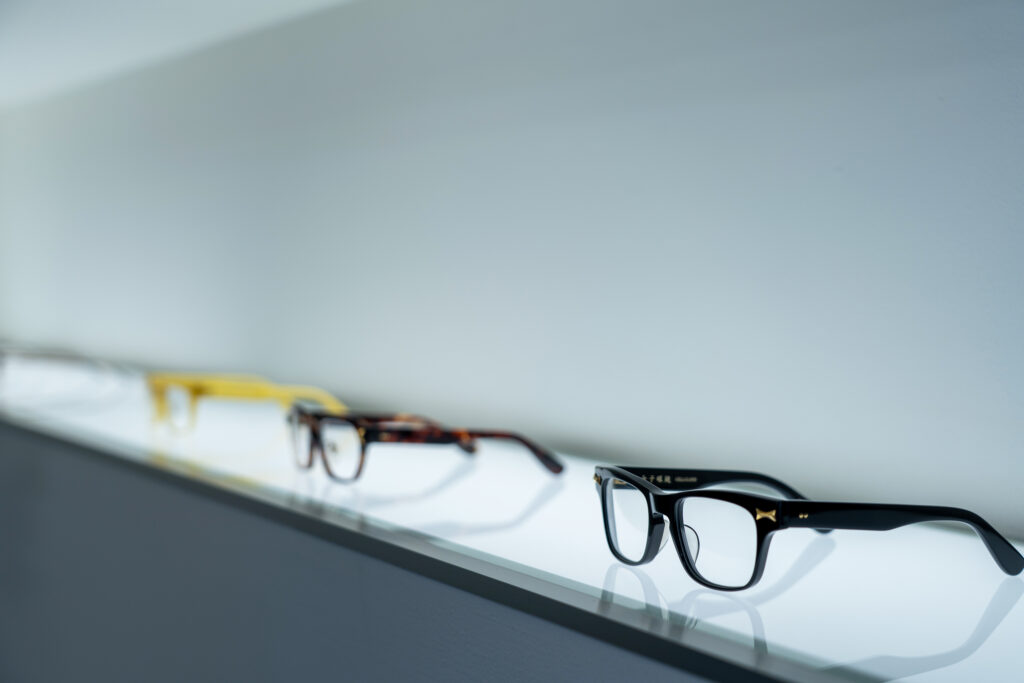
自分たちがつくらなければ
自社ブランドの商品開発が軌道に乗り、販路が開拓できたものの、新たに課題となったのが製造の安定性でした。
2000年代、中国製の商品の流通によって価格競争が激化し、鯖江の工場や職人は仕事を奪われていきました。廃業を免れた一部の工場に注文が集中。金子眼鏡が製造を委託していた取引先でも、納期や品質の面で問題が起きるようになりました。このとき、自社ビジネスの危機感だけでなく、産地全体が危ないという焦りが生まれたといいます。
「当社は規模が小さかったうえにディテールにこだわっていたので、外資系の大手からドンと発注が入ると、そちらの製造を優先されてしまう。安定した製造元を探すため、鯖江の工場や職人さんにお願いして回っていたら、聞こえてくるのは後継者不足や廃業の懸念ばかりでした」(市川さん)
「特にプラスチックフレームは、木工製品をつくるように素材を削り出し、組み合わせ、磨く手間がかかるので、人手不足は致命的です。それならば自分たちでプラスチックフレームをつくれるようになろう。そう覚悟するのは必然的な流れでした」
廃業した工場で始めた眼鏡づくり
2006年、市川さんを中心に製造部門が発足。といっても、廃業した眼鏡工場を借り、ゼロからスタートしたものづくりでした。まずはつるの部分から、それができたらフロントの部分を。機械を1台ずつ揃えて、工程を増やしていきました。
Seigo Ito
3年後の2009年、一通りの工程ができるようになったところで「BACKSTAGE」を設立しました。商品企画、デザイン、色決め、素材の切削、加工、研磨、組み立て、調整、検品まですべての工程が一貫してできる拠点工場です。
「デザイナーと職人が同じ工場にいるため、お互いを尊重しながら意見交換できるのが特徴です。デザイナーも、自分で眼鏡をつくろうと思えばつくれますし」と大橋さん。スタッフがすべての工程をひと通り担えるようになっているのも、一貫生産ならではの強みです。
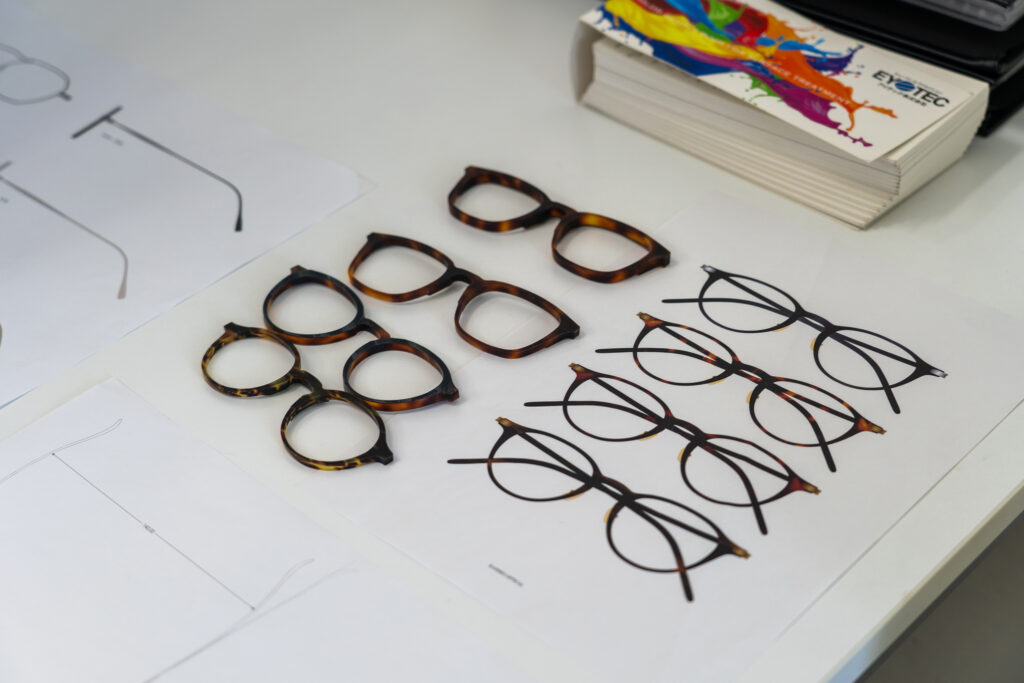
Seigo Ito
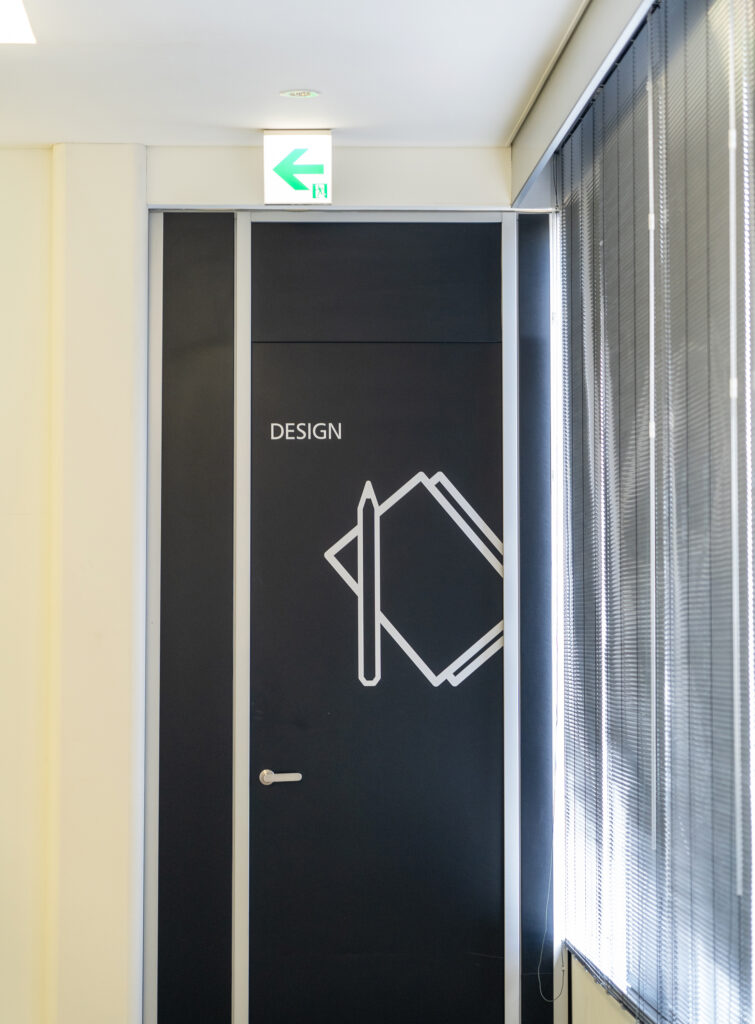
人から機械へ、機械から人へ
眼鏡づくりの最初の工程は、職人の手でおこなわれます。
プラスチックフレームの原材料であるアセテートやセルロイドは、厚さ数ミリの板状で納品されます。これを眼鏡のフロントやつるのサイズに合わせて長方形に切り出した後、1枚ずつ金型に挟んでプレスして顔面に沿ったカーブをつけます。
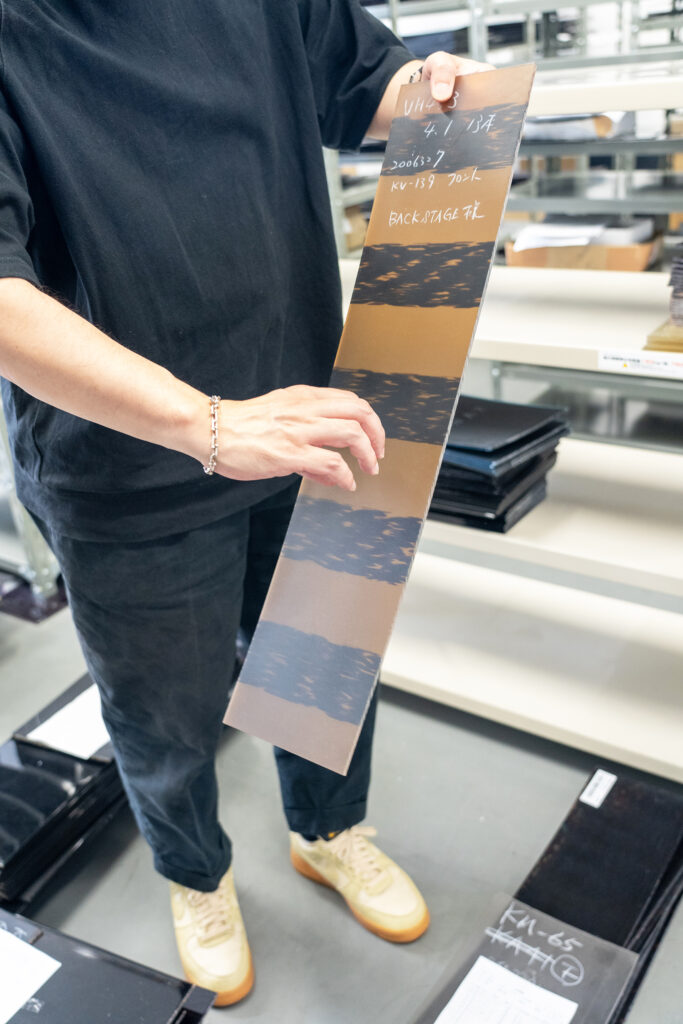
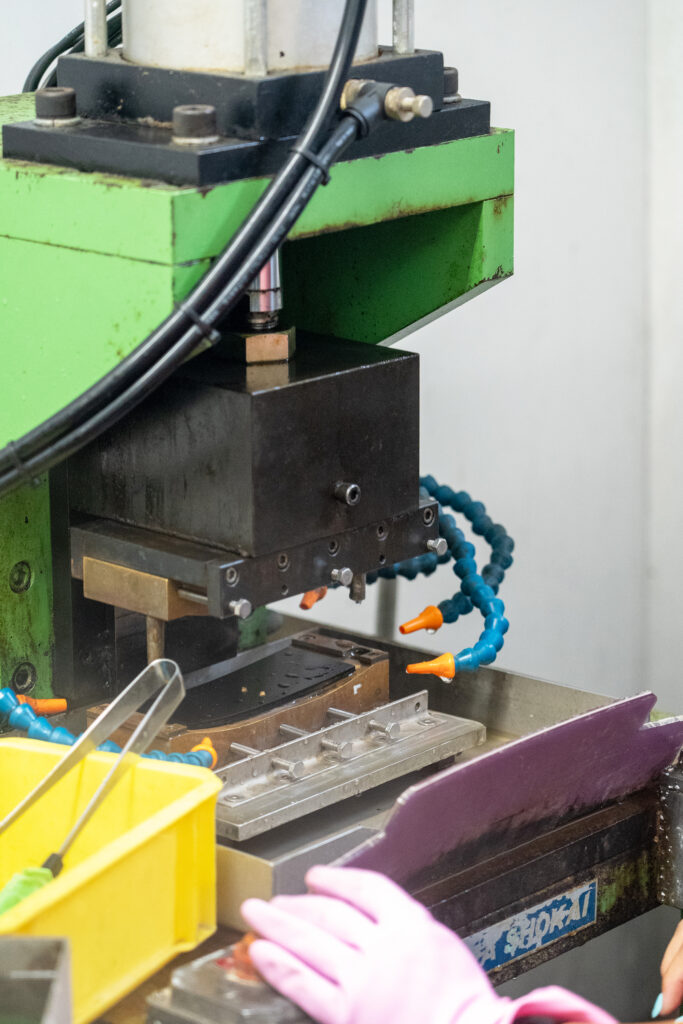
Seigo Ito
これらをBASEMENTに運んで機械を使って眼鏡の形に削り出し、ロボット研磨を経たのち、再びBACKSTAGEに戻して、改めて人の手でつるの芯入れや研磨をして仕上げます。ただ、BASEMENTのほうでも機械の調整や操作、製品の運搬や削りくずの掃除など、人による作業は欠かせません。機械が担っているのは、一部の作業に過ぎないのです。
「眼鏡づくりはほとんどが手作業によるものです。ロボットの力を借りて労働集約型産業から脱却していくことは、これから先も眼鏡づくりを発展させ続けるためには必要な変化だと考えています」(大橋さん)
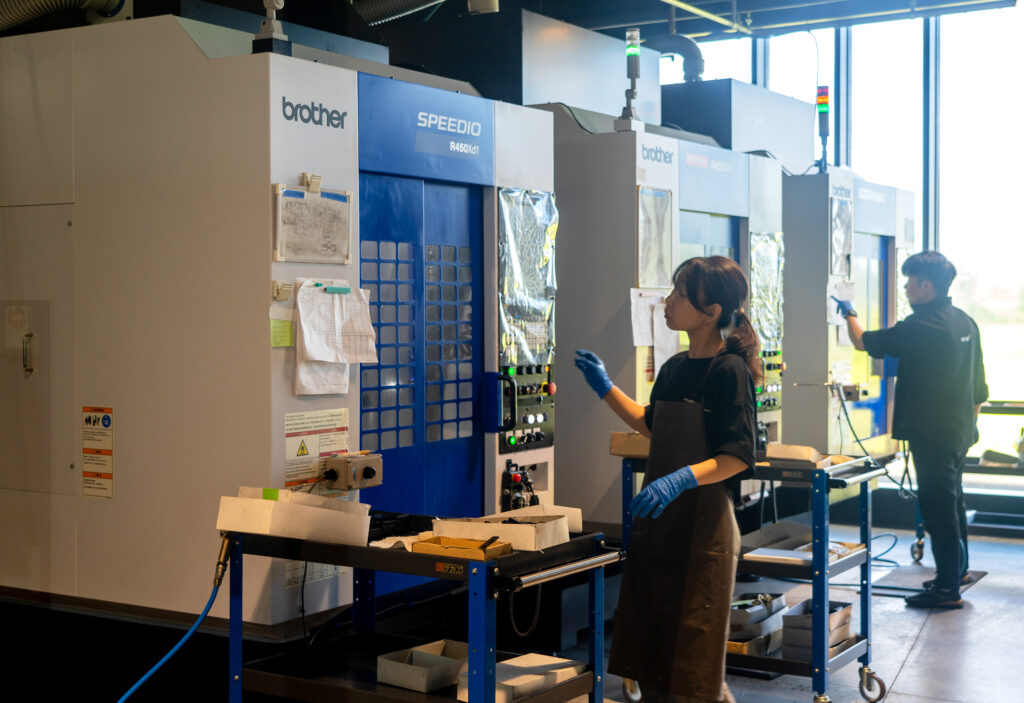
Seigo Ito
手仕事と機械を融合させる
大橋さんは「ロボットを使うのはコストや時間の節約が目的ではない。よりよい製品をつくり、技術を高めるため」と強調します。あくまで眼鏡づくりの未来のため。労働人口が減る中で、グローバル化による技術革新や価格競争に対抗し、眼鏡産地としての鯖江を残していくためだ、と。
「もちろんロボットの力を借りたとしても、丁寧なものづくりをすることに変わりはありません。考え方としては、一流のシェフが料理をつくるけれど、キャベツの千切りだけは機械に任せてもいいんじゃないかというような。大事なところに集中できるようにし、熟練の職人たちが一つひとつ手作業で仕上げています」
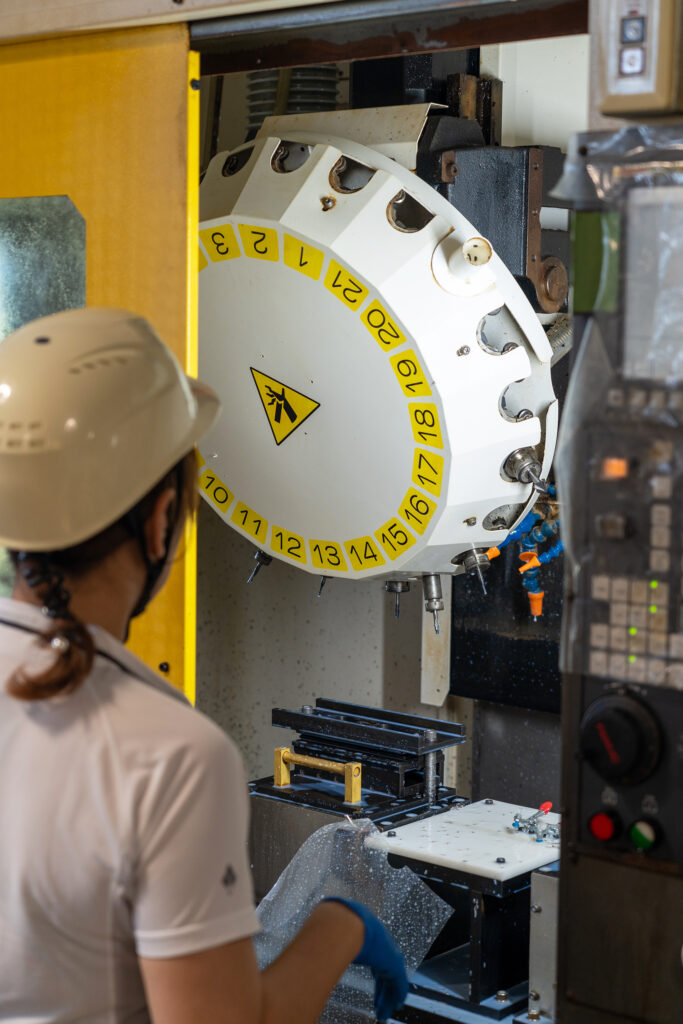
いまやどんな仕事であっても、ロボットやAIが代替する可能性に直面しています。それにより、人間にしかできない仕事の質がより研ぎ澄まされ、唯一無二の価値が生まれるという側面もあります。
金子眼鏡でのそれは、「バフ研磨」という工程だそう。プラスチックフレームに独特の艶と光沢を生み出す昔ながらの技術です。機械では代わることができない、人から人へ受け継ぐべき手仕事として、すべてのスタッフが習得しています。
その継承は、眼鏡の品質だけでなく、職人たちの精神も支えているのだといいます。【後編に続く】
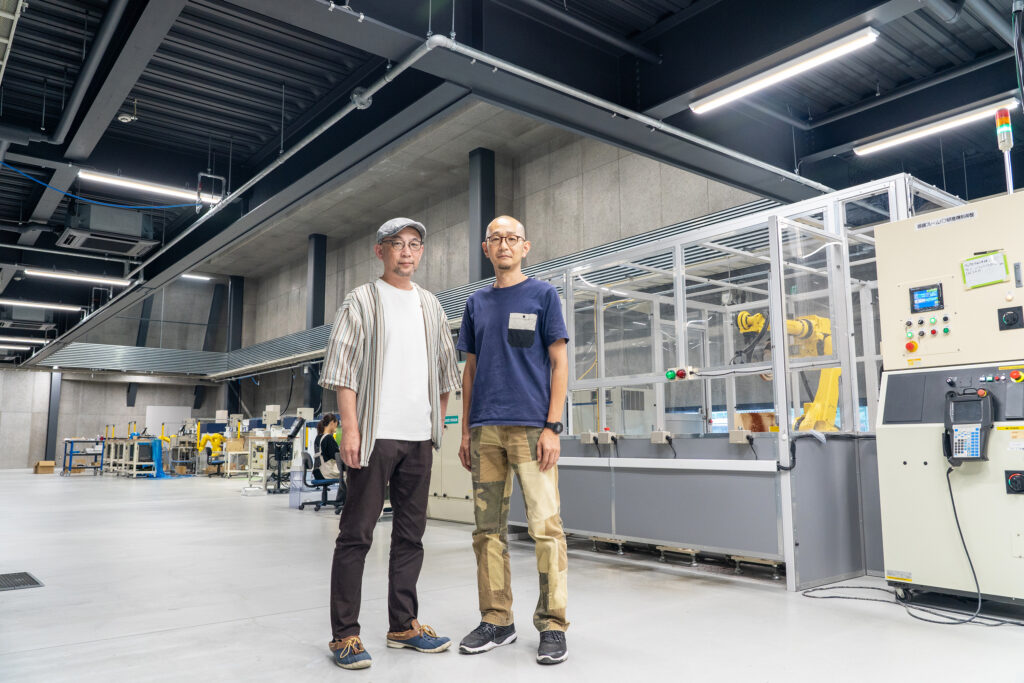
Seigo Ito
【後編はこちら】「私たちは眼鏡をつくっている」 シンプルな言葉の真意とは。金子眼鏡が、磨きに込める美意識
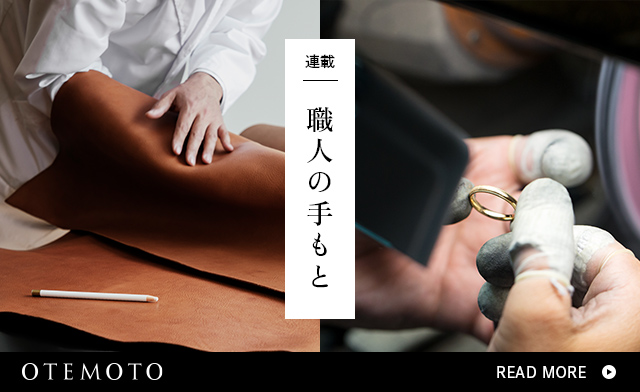
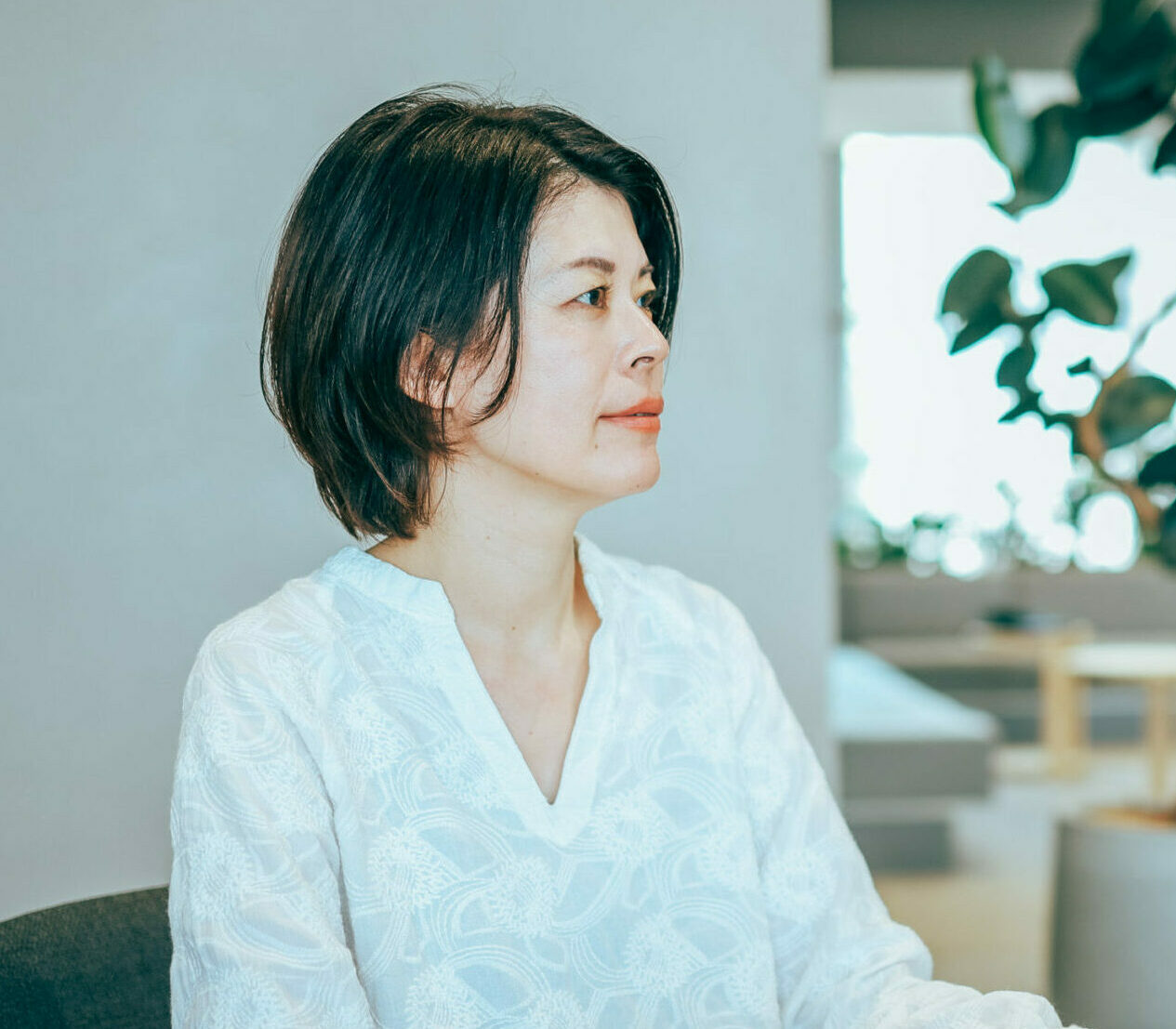